Continuous Improvement - Bharat Forge Limited, Pune. (India)
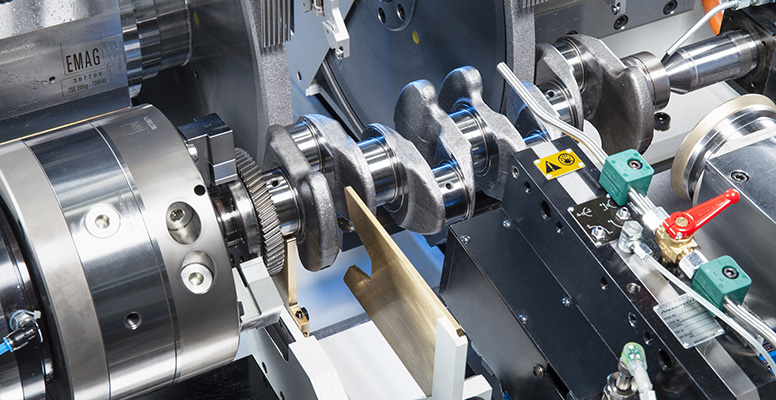
Bharat Forge Limited (BFL), the Pune based Indian multinational is a technology driven global leader in metal forming having transcontinental presence across nine manufacturing locations, serving several sectors including automotive, power, oil and gas, construction & mining , locomotive, marine and aerospace. Part of Kalyani Group - a USD 2.5 billion conglomerate with 10,000 global work force; BFL today has the largest repository of metallurgical knowledge in the region and offers full service supply capability to its geographically dispersed marquee customers from concept to product design, engineering, manufacturing, testing and validation. The world's largest forging company with manufacturing facilities spread across India, Germany, Sweden and France, Bharat Forge manufactures a wide range of high performance, critical & safety components for the automotive & non-automotive sector. It is India's largest manufacturer and exporter of automotive components and leading chassis component manufacturer in the world. BFL's customer base includes virtually every global automotive backed by several decades of experience in component manufacturing & metallurgy.
For setting up lines for Crankshafts, Connecting Rod, Knuckles, Axel beams, we used the tool of Process Improvement.
We identified the various processes to manufacture a Finished Good. We identified that few operations can be clubbed on a single Work center. This will reduce time, Cost, & increase capacity as well.
A typical crank shaft manufacturing involves, Inclined Oil hole drilling on Pin & straight oil hole drilling on Journal. These holes intersect each other. We identified these operations can be combined with a fully automated Machine. We suggest them EMAG GMBH work center for both the operations.
We found that there are 2 different operations of Grinding involved. They are Journal Grinding & Pin Grinding. We identified these operations can be clubbed together & can be performed on Single fully automated Machine. We suggest them Junker GMBH Work center for both the operations.
We assist BFL in FG packing areas as well. We identified & suggested the time line on crankshaft oil dipping operation, which is used to stop corrosion.